Design and Control of a 3-DoF Linear Delta Manipulator
Jakub Kaminski
About the project
The delta manipulator was my individual B.Sc. project at the Poznan University of Technology, Poland. My primary interests concerning this robot were solving its kinematics and optimizing its working area to a desired shape based on mechanical constraints. Then, I designed the structure of the robot using SolidWorks, and manufactured several robot components on my CNC milling machine. Finally, I implemented the kinematics in C++, integrated it with the LinuxCNC control system, assembled the robot, and tested the robot with a sample pick-and-place task. My project was meant to be a cheaper, experimental alternative to the Festo Tripod linear delta, featuring 50% of its operational speed at 3% of the cost.
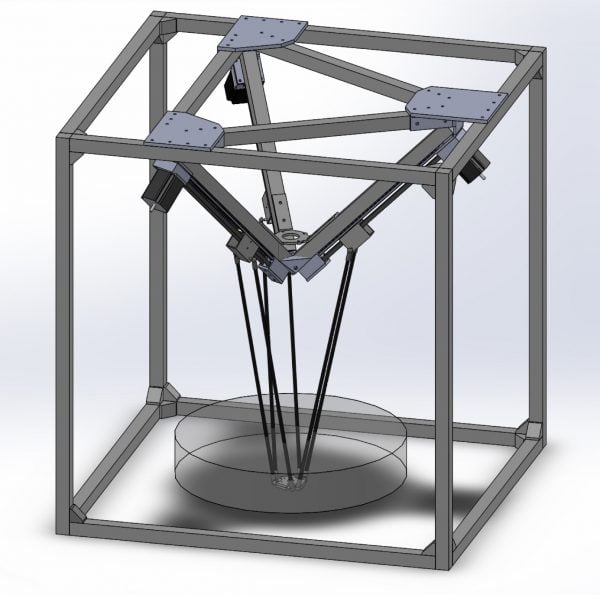
Value Proposition
The parallel delta robot kinematics was originally proposed by R. Clavel [ref]. In comparison to the most common delta-type parallel manipulators with 3 rotary axes, the linear delta manipulator uses linear DoFs and offers even lower inertia of its movable components. In the industrial setting, this type of robot can be placed in a light, screwed aluminum frame, much easier to build than steel-based welded frames used for conventional, rotary-type delta manipulators. The design is based on 3 convergent linear actuators that reduce the number of links subjected to bending forces. As a result, this design enables manipulation and assembly tasks requiring high Z-axial pressing force. As far as cost-effective solutions are concerned, high-resolution motion is much easier to achieve with linear rails than with rotary axes. This contributes to the high popularity of the linear-rail-based delta designs in consumer-grade 3D printing.
Mechanical Design and Manufacturing
Robot Components:
1. Aluminum Extrusion
2. Motor mount [CNC-machined]
3. Stepper motor [1,9Nm, NEMA23 size]
4. Timing belt [HTD3M]
5. Rotary axis adapter
6. Bracket with pulley
7. Mounting plate
8. Top mounting bracket
9. Linear rail
10. Linear carriage
11. Robot arm
12. End-effector platform
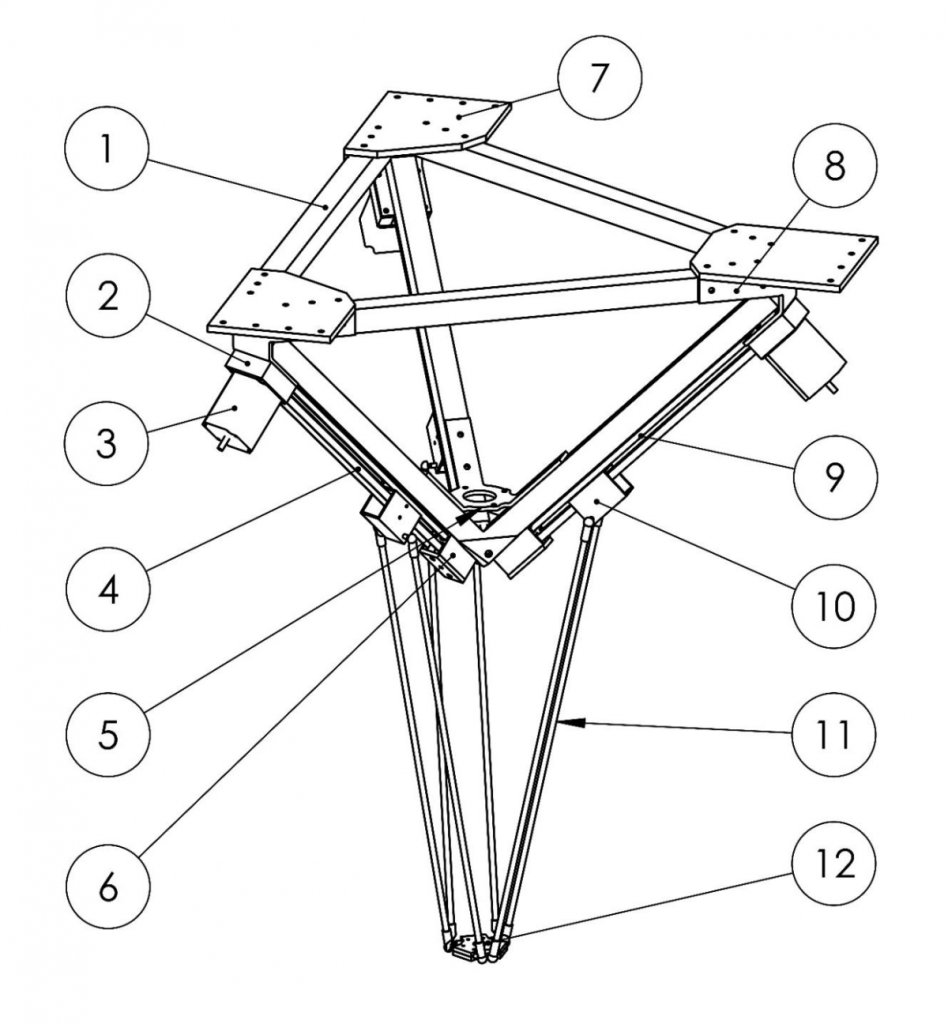
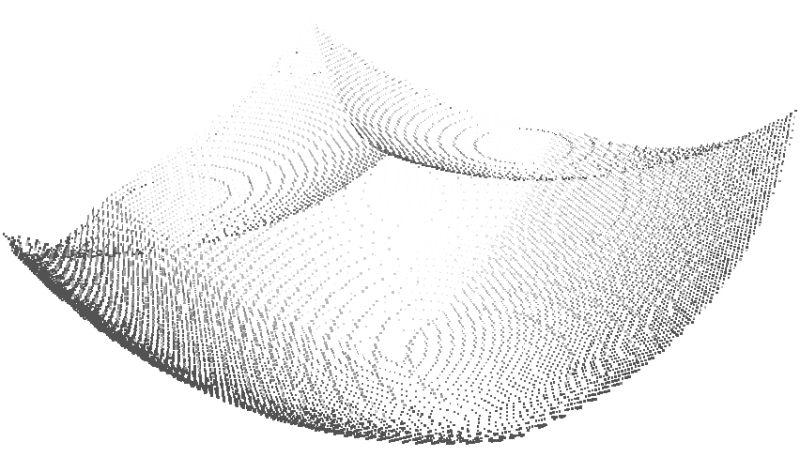
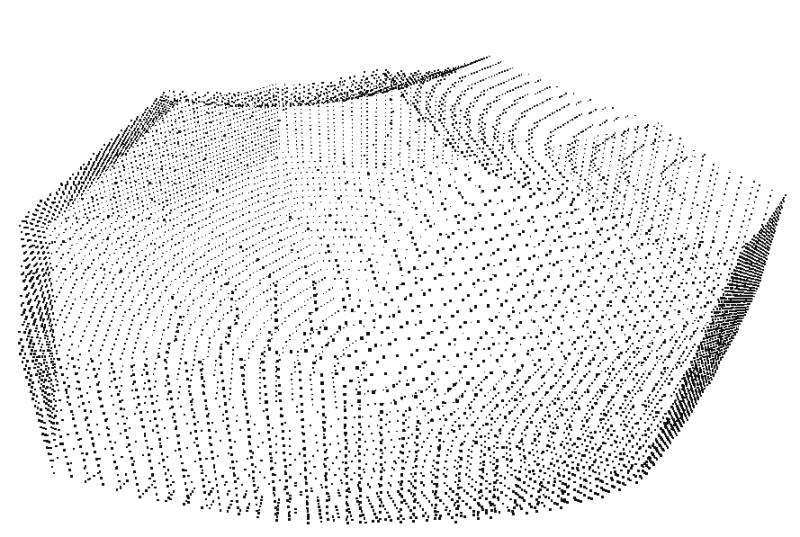
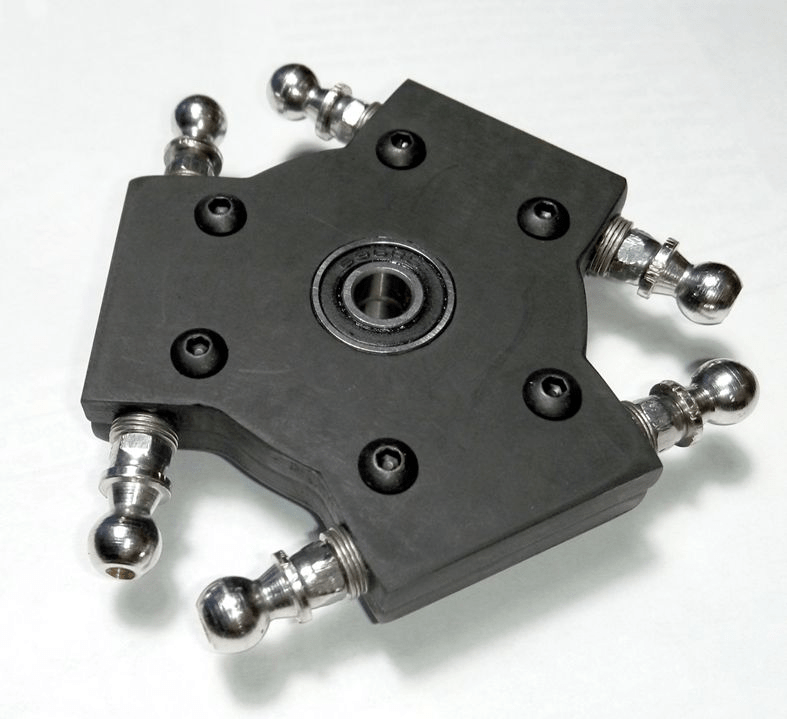
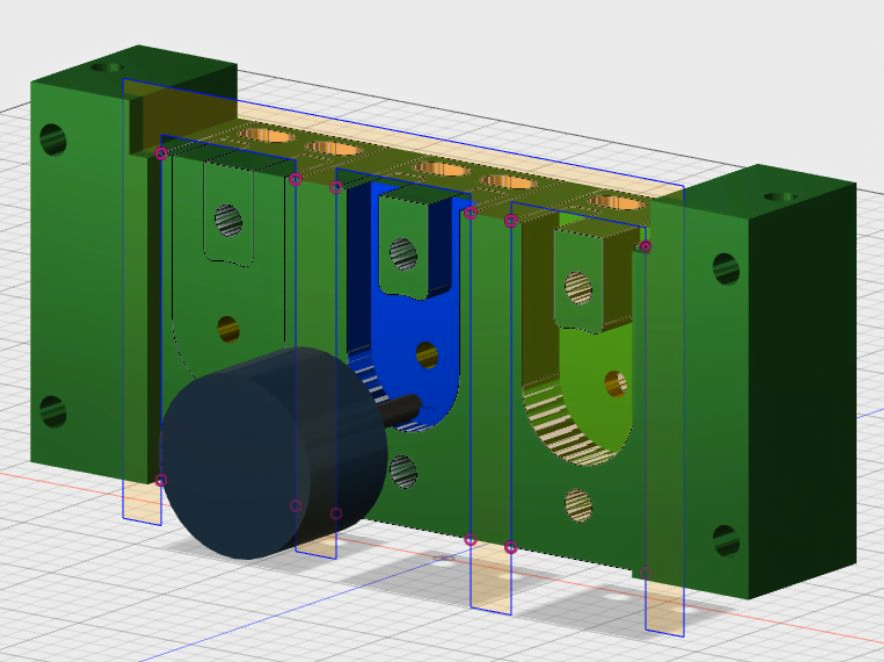
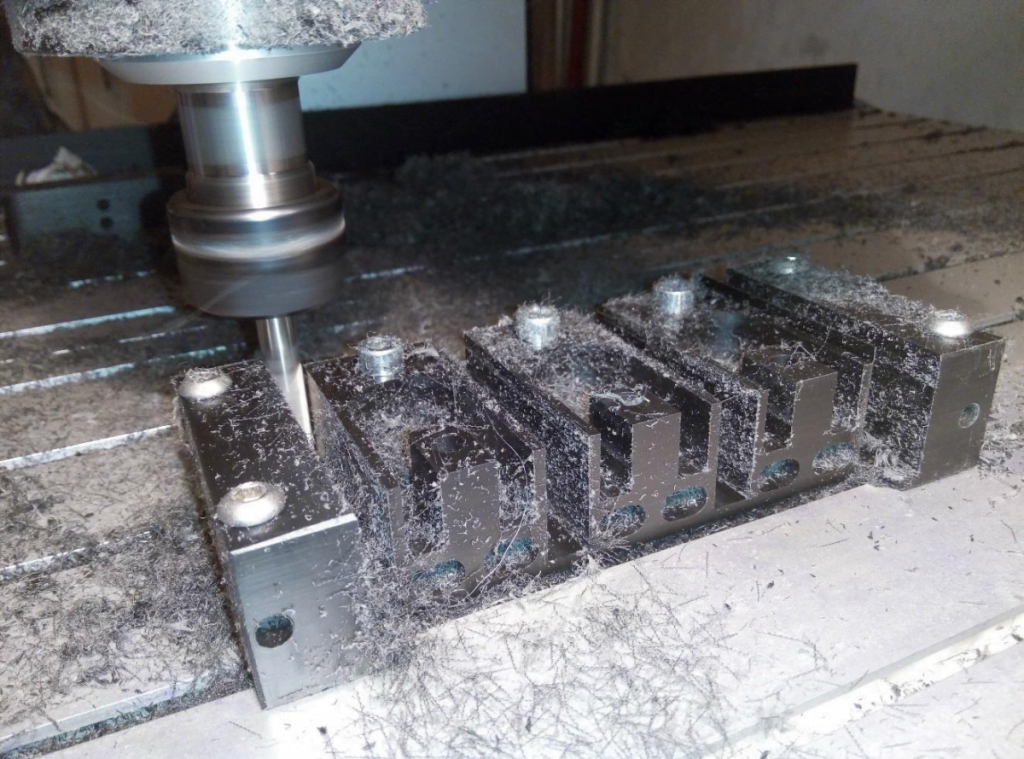
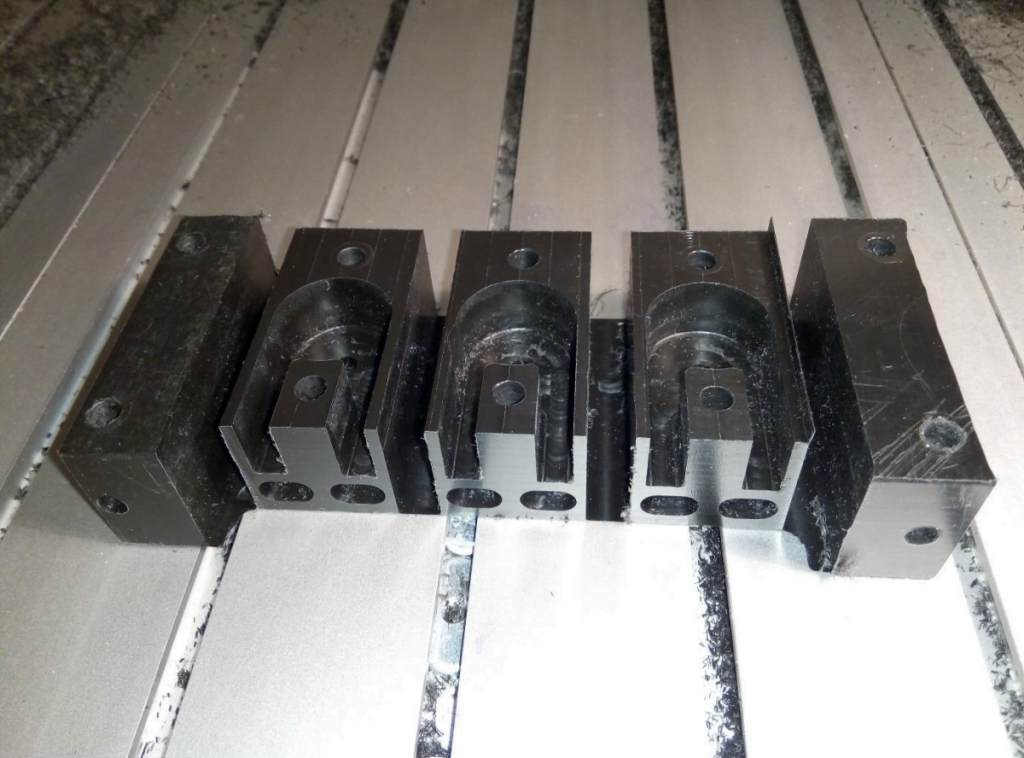
Performance Testing
The robot achieved…
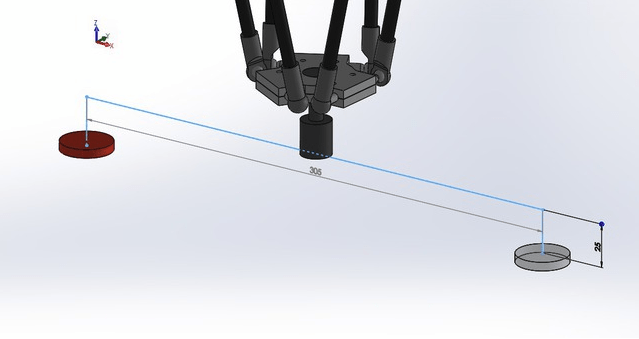
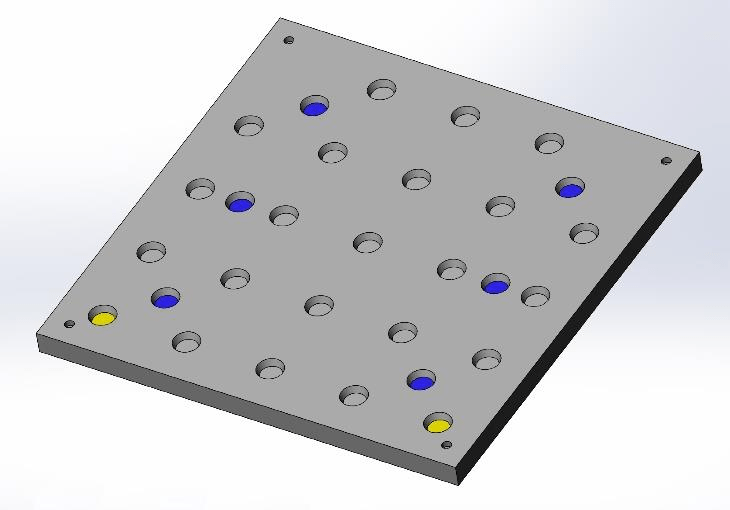